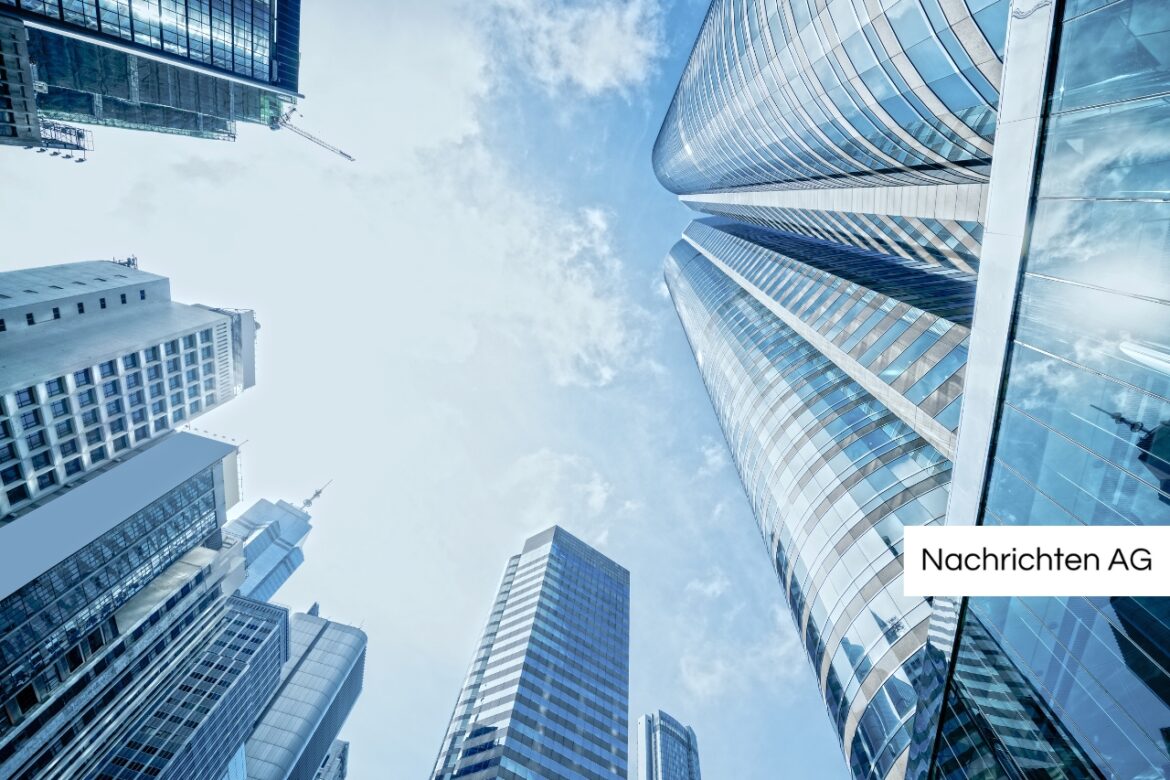
In den letzten Jahren hat sich das Verhältnis zwischen den USA und Europa in vielen Wirtschaftsbereichen gewandelt. Peter Leibinger, der Präsident des Bundesverbands der Deutschen Industrie (BDI), hebt hervor, dass die USA in mehreren industriellen Sektoren stark auf Europa angewiesen sind. Insbesondere im Maschinenbau werden rund 70 Prozent der Präzisionsteile in den USA mit europäischen Maschinen produziert. Leibinger ermerkt, dass es in den USA kaum Hersteller von Werkzeugmaschinen gibt, was die Abhängigkeit weiter verstärkt. In diesem Kontext beschreibt er die USA als „schwierigen Kunden“ und betont die Notwendigkeit eines aktiven Dialogs zwischen Europa und den USA.
Leibinger fordert die EU auf, ihre „Instrumente“ zu kennen und gegebenenfalls anzuwenden, um die eigenen Interessen zu wahren. Dies wird besonders relevant im Hinblick auf Prozess-Sensorik, ein weiterer Bereich, in dem die USA auf europäische Technologien angewiesen sind, insbesondere für Raffinerien und Pharmawerke. Hierbei betont er, dass Gegenzölle nur als letztes Mittel in Betracht gezogen werden sollten; stattdessen seien Verhandlungen der bevorzugte Weg.
Industrie 4.0 und ihre Bedeutung
Der Wandel in der Industrie wird auch durch die Digitalisierung und Automatisierung vorangetrieben, die mit dem Begriff „Industrie 4.0“ zusammengefasst wird. Diese vierte industrielle Revolution, die erstmals 2011 auf der Hannover Messe vorgestellt wurde, ist Teil einer hochmodernen Strategie der deutschen Bundesregierung zur Förderung der Digitalisierung in der Industrie. Industrie 4.0 zielt darauf ab, die Produktion durch die Integration moderner Informations- und Kommunikationstechnologien sowie das Internet der Dinge (IoT) zu optimieren.
Ein zentrales Element dieser Transformation ist die Nutzung präziser und zuverlässiger Daten. Diese sind entscheidend für den Erfolg der Industrie 4.0, da ungenaue Messwerte zu Produktionsfehlern, ineffizienten Abläufen und kostspieligen Stillständen führen können. Moderne Messtechnik ermöglicht die Echtzeitüberwachung von Maschinen, die frühzeitige Erkennung von Abweichungen und die Durchführung vorausschauender Wartung.
Fünf Schritte zur Implementierung von Industrie 4.0
- Analyse der bestehenden Systeme: Bestandsaufnahme der eingesetzten Sensoren und Messtechnologien.
- Technologieauswahl: Auswahl der passenden Messtechnik je nach Produktionsanforderungen.
- Integration neuer Technologien: Reibungslose Einbindung neuer Systeme in bestehende Prozesse.
- Weiterbildung der Mitarbeitenden: Schulungen zur effektiven Nutzung neuer Systeme.
- Kontinuierliche Optimierung: Regelmäßige Analyse und Anpassung der Prozesse.
Die Bedeutung von präziser Messtechnik reicht über Effizienzsteigerung hinaus; sie ist auch ein Schlüssel zur Nachhaltigkeit. Der optimale Einsatz von Ressourcen führt nicht nur zu Kosteneinsparungen, sondern auch zu einer Reduzierung des Material- und Energieverbrauchs. Unternehmen können dadurch Nachhaltigkeitsziele deutlich kommunizieren und Vertrauen bei Stakeholdern gewinnen.
Mit der fortschreitenden Integration von IoT und Künstlicher Intelligenz gestalten sich die Produktionsprozesse nicht nur effizienter, sondern auch flexibler und individueller. Industrie 4.0 steht damit auch für die Zukunft der industriellen Produktion – eine Zukunft, in der Maschinen intelligent miteinander kommunizieren und sich an wechselnde Anforderungen anpassen können, eine Entwicklung, die die Industrie für die kommenden Jahrzehnte prägen wird.
Zusammengefasst ist die Zusammenarbeit zwischen den USA und Europa im industriellen Bereich nicht nur von finanziellen Interessen geprägt, sondern auch von der Notwendigkeit, sich den Herausforderungen der neuen industriellen Revolution zu stellen. Die Abhängigkeit der USA von europäischen Technologien sollte als Chance für eine vertiefte Kooperation betrachtet werden.
ZVW berichtet, dass dies… Umweltdialog und Inno-Focus ergänzen, dass…